焊接作為汽車整車生產工藝中的重要環節,自動化程度是衡量整車廠生產水平的標志,今年九月焊接機器人的安裝到位,神龍成都工廠焊接自動化率達到百分之百,這一技術水平將在國內遙遙領先。沖壓車間內,最大承重達80噸的天車,在15.4米的高空吊裝設備。先進的沖壓設備,兩條生產線,4臺沖壓設備,總價值約4億元!這些設備的先進之處就在于,將汽車覆蓋件的生產節拍,從每分鐘8—10片提高到15—20片。沖壓設備采用濟南二機床。
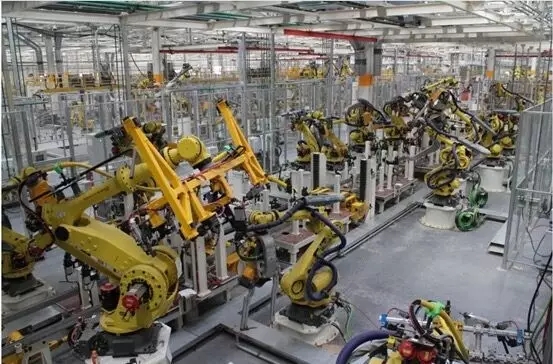
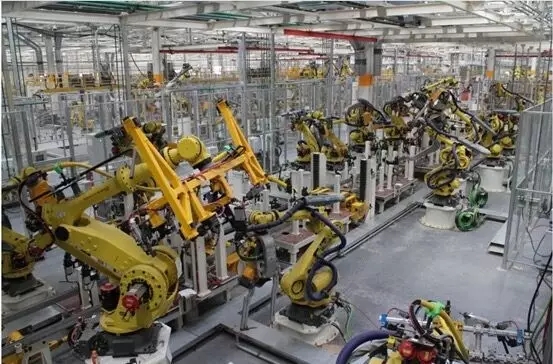
10月10號,神龍汽車成都工廠傳出消息,焊裝車間車身線于當日打通,標志著焊裝車身線具有線外批量生產的能力。據介紹,焊裝采用的激光焊技術是近年來新興的焊接技術,成都工廠在開啟件、前后端、車身線都采用激光釬焊、激光熔焊技術。焊裝生產線主線全部柔性化設計,可以隨機生產6種車型,柔性切換,設計節拍60臺/時。435臺機器人打造的100%自動化率高效率工廠直接生產工人不到100人,僅為同等規模傳統汽車制造廠的1/10,工人勞動強度顯著下降,勞動生產率大幅提高。自動化程度是焊接車間的最大特點。一輛白車身的廠內焊點達到2400多個,而整個通過320個機器人、81個夾具、44個轉臺,就能完成相關車型的生產任務。主車間實際操作人員僅75人,不足機器人數量的四分之一。
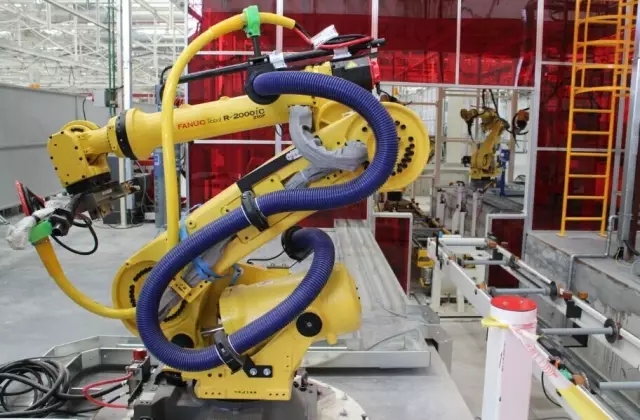
達產后每分鐘可下線一臺車
成都工廠焊裝生產線廣泛采用了目前汽車制造先進工藝和技術:激光熔焊/釬焊、自動弧焊、機器人螺柱焊、中頻焊、無釘沖鉚、自動防飛濺噴淋、高速輸送輥床等,先進工藝技術的采用顯著提高了產品質量,減少了返修,提高了生產率。成都工廠焊裝工藝技術處于國內領先水平。
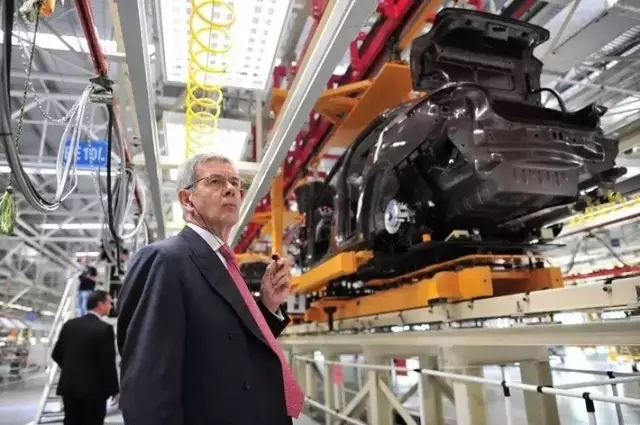
“一般來說在國內生產的合資廠商,焊裝自動化率在50%左右,我們的焊裝車間自動化率達到100%。處于世界領先狀況?!焙附榆囬g負責人孫繼勝表示。據透露,車間采用機器人生產后,人工工位基本消失。車間的圍欄由傳統的鐵絲網圍欄換成了先進高分子PC透明塑料板,PC板視覺效果好,其不僅可以全方位隔絕人員進入,還兼有防火的功能。東風神龍成都項目于去年10月奠基,預計2016年建成投產,將貢獻36萬輛的產能,主要生產東風雪鐵龍、東風標致和東風三個品牌車型,以高端SUV、MPV為主,車型與歐洲同步開發、同步投放。
據了解, 神龍汽車公司 成都乘車用項目位于成都市龍泉驛區,規劃總投資123億元,規劃總產能32萬輛,其中一期工程總投資79.05億元。